ET EPOXY-COATED
TMT BARS
These are long life, high corrosion-resistant, fusion-bonded epoxy-coated TMT bars.
A fusion-bonded epoxy layer is coated electrostatically on pre-heated TMT bars (and
cured) to deliver high protection from corrosive elements. Fusion-bonded epoxy is
an excellent insulator and acts as a barrier to the entry of chloride ions. This
enhances the life of steel bars.
A fusion-bonded epoxy layer is coated electrostatically on pre-heated TMT bars (and
cured) to deliver high protection from corrosive elements. Fusion-bonded epoxy is
an excellent insulator and acts as a barrier to the entry of chloride ions. This
enhances the life of steel bars.
These are long life, high corrosion-resistant, fusion-bonded epoxy-coated TMT bars. A fusion-bonded epoxy layer is coated electrostatically on pre-heated TMT bars (and cured) to deliver high protection from corrosive elements. Fusion-bonded epoxy is an excellent insulator and acts as a barrier to the entry of chloride ions. This enhances the life of steel bars.
Available For
ET CRS TMT BARS
CRS Fe 500
CRS Fe 500 D
CRS Fe 550
CRS Fe 550 D
CRS Fe 600
ET REFINED STEEL TMT BARS
Fe 500 D
Fe 500
Fe 550 D
Fe 600
ET SUPERIOR QUALITY STEEL TMT BARS
Fe 500
Advantages
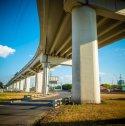
Epoxy-coated bars have twelve times longer life than bare TMT bars.
Epoxy-coated bars have twelve times longer life than bare TMT bars.
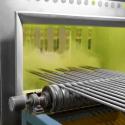
Factory-based application ensures a uniform thickness of the coating.
Factory-based application ensures a uniform thickness of the coating.
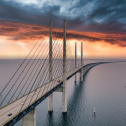
Epoxy coating is an environment-friendly sustainable solution and adds
excellent adhesive capacity to steel bars.
excellent adhesive capacity to steel bars.
Epoxy coating is an environment-friendly sustainable solution and adds excellent adhesive capacity to steel bars.
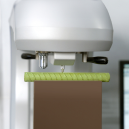
Multi-stage spectrometry testing done to check purity
of steel at every stage
of steel at every stage
Multi-stage spectrometry testing done to check purity
of steel at every stage
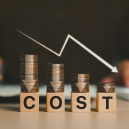
Highly cost-effective. Adding an epoxy layer to bars does not add much to
the cost burden. Lowers the cost of labour, as the bars require little or no
maintenance.
the cost burden. Lowers the cost of labour, as the bars require little or no
maintenance.
Highly cost-effective. Adding an epoxy layer to bars does not add much to the cost burden. Lowers the cost of labour, as the bars require little or no maintenance.
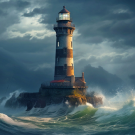
Ideal for use in all infrastructure and construction projects. Special
application in marine infrastructure.
application in marine infrastructure.
Ideal for use in all infrastructure and construction projects. Special application in marine infrastructure.
ET EPOXY TMT BARS
Properties
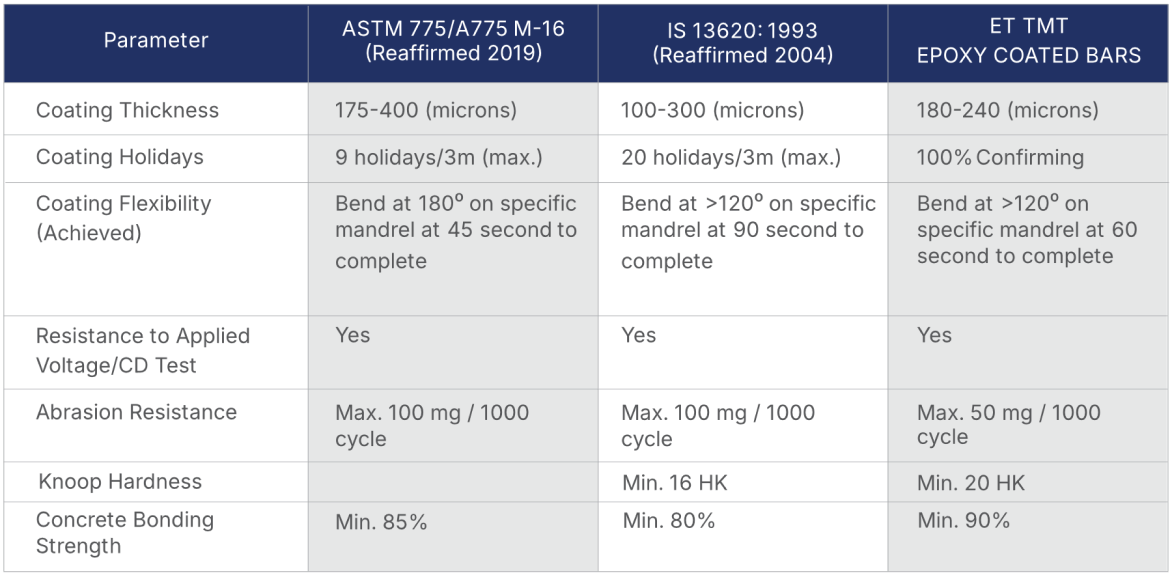
Other ET TMT Products
Have Questions? Call us Now
Sales: +91 8238079223
Need Support? Write to us
salestmt@electrotherm.com