ET CUT & BEND
TMT BARS
ET cut and bend TMT bars are corrosion-resistant, high-yield strength,
ductile TMT bars in pre-fabricated ready-to-use cut & bend format. They
are available in all ET TMT Bar grades.
ductile TMT bars in pre-fabricated ready-to-use cut & bend format. They
are available in all ET TMT Bar grades.
ET cut and bend TMT bars are corrosion-resistant, high-yield strength, ductile TMT bars in pre-fabricated ready-to-use cut & bend format. They are available in all ET TMT Bar grades.
Advantages
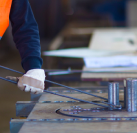
Automatic Italian Schnell machines ensure cutting and
bending efficiency, accuracy and uniformity.
bending efficiency, accuracy and uniformity.
Automatic Italian Schnell machines ensure cutting and
bending efficiency, accuracy and uniformity.
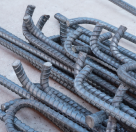
High force resistance and ductility. Ductility enables cutting
and bending sans wear and tear.
and bending sans wear and tear.
High force resistance and ductility. Ductility enables cutting
and bending sans wear and tear.
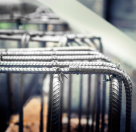
Perfect joints with closed-loop reinforcement for lateral support.
Provide shear reinforcement in beams.
Provide shear reinforcement in beams.
Perfect joints with closed-loop reinforcement for lateral support.
Provide shear reinforcement in beams.
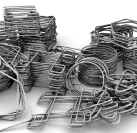
Available in superior finish in all desired angles and shapes in
CNC bars, refined steel bars and superior steel bars.
CNC bars, refined steel bars and superior steel bars.
Available in superior finish in all desired angles and shapes in
CNC bars, refined steel bars and superior steel bars.
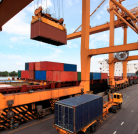
The customer pays only for the theoretical blueprint weight. Savings on
freight and on cumbersome handling and wastage in onsite cutting
and bending.
freight and on cumbersome handling and wastage in onsite cutting
and bending.
The customer pays only for the theoretical blueprint weight. Savings on freight and on cumbersome handling and wastage in onsite cutting
and bending.
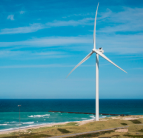
Best suited for critical design structures such as windmills, flyovers,
bridges, etc.
bridges, etc.
Best suited for critical design structures such as windmills, flyovers, bridges, etc.
Other ET TMT Products
Have Questions? Call us Now
Sales: +91 8238079223
Need Support? Write to us
salestmt@electrotherm.com